For the last 10 years, KinsBrae Packaging has been trying to figure out how to disrupt the world and create a better and more efficient system for its customers.
Now with its first-of-a-kind paper bottle machine, the company is hoping to change how consumers and companies look at bottles and enjoy some of their favourite drinks.
Having started in a garage in Waterloo back in 2014, founder and president Shawn Bonnick had a goal of centralizing and becoming a one-stop shop for all things packaging.
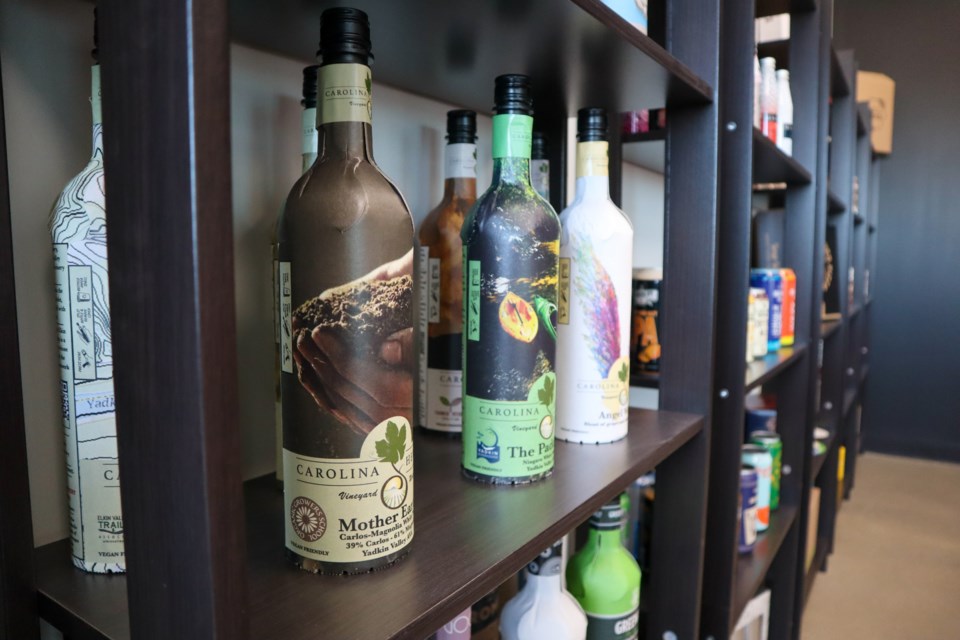
"When the company I was working for before got sold, it seemed like the perfect opportunity for me to say, let's give this a shot on my own," said Bonnick. "So my original intent was to work out of my house and be a distributor and connect all facets of the packaging."
The plan quickly changed when the company started to grow and they needed space for storage. This would also allow them to bring services they once outsourced in-house like graphic printing.
"I've always wanted to flip the script on how things were done and even with the paper bottle, this isn't new technology, but no one has ever had the capability to use it," said Bonnick.
Working with Frugal Industries out of the United Kingdom, KinsBrae was the first company to import and utilize one of the UK company's fully automated paper bottle machines.
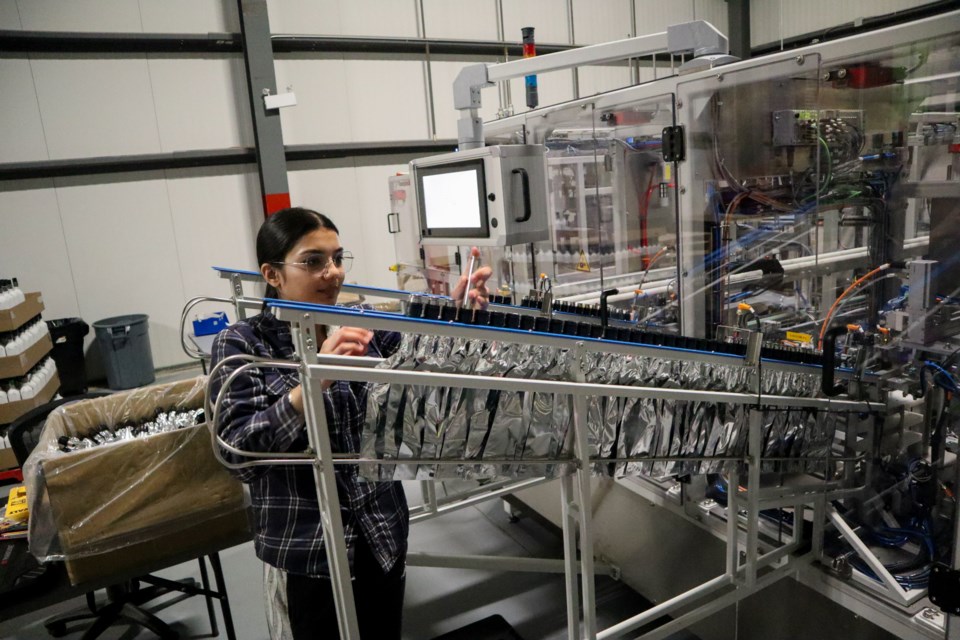
One of the first things that caught Bonnick's eye about the paper bottle was the environmental aspects and the ability to recycle the product.
"Going through the whole process was like, okay, this makes a lot of sense for us," added Honnick. "We all know glass is also recyclable, but the paper bottle is something you can bring anywhere and when you're done the bag pops out and into the blue bin it goes."
The bottles start as 100 per cent recycled cardboard printed and cut into templates that can have any graphic printed 360 degrees around the bottle.
The bottle can only be used for non-carbonated liquids such as wine, juice and iced coffee. The bag that sits inside the bottle is not strong enough at this time to handle the pressure from a carbonated liquid like beer or certain coolers.
"The potential is almost endless," said Dennis Lubbers VP of process and manufacturing. "We're really just getting started with exploring what we can do with this technology and it's already growing."
Having just turned on the machine last month, KinsBrae is in the process of mapping out where its second and third machines will go.
Lubbers said the environmentally friendly aspect of the bottle is not the only thing that makes it special.
"We can stack the bottles higher and they weigh significantly less than glass," he said. "We're able to ship nearly double the amount with the paper bottles versus glass."
Since paper bottles weigh five times less than glass, KinsBrae can maximize how much product they can fit on a truck. There is also no breakage with paper, so they can eliminate the inserts that prevent glass bottles from hitting each other and shattering during transport.
The impressive machine is fully automated and can produce up to 500 bottles an hour. The only human interaction needed is to load the machine and can be operated by a single person.
As the paper templates go through the machine, robotic arms glue, press and shape the bottles until a finished product flies off a conveyor belt down the other end.
"It's quite amazing once you really see it get going," said Honnick. "We can produce approximately five million bottles off of it. With three machines, we'll be able to produce 15 million bottles annually, which is still just a drop in the bucket."
KinsBrae already creates packaging for companies such as G Fuel, Farmboy and other leaders in the global wine and liquor market. Honnick adds that they are in the works to bring in some other big players over to the paper bottle and customers can expect to see them on shelves everywhere.
"There's nothing we can make official yet, but a lot of the staples you might have in your cupboard, you'll probably see in a paper bottle very shortly."